Fiber-rope Retrofit Extends Subsea Crane Capabilities
MacGregor, part of Cargotec, has launched a fiber-rope retrofit option for its subsea cranes; the modular upgrade replaces the crane's original steel wire rope with synthetic fiber rope, using the same technology as MacGregor’s fiber-rope crane, the FiberTrac 1500, introduced earlier this year. These cranes combine MacGregor's offshore crane technology with the fiber-rope tensioning technology perfected by Parkburn Precision Handling Systems.
Maintaining and Surveying Steel Wire Ropes
An incident investigated by the New Zealand Transport Accident Investigation Commission (TAIC) has highlighted the importance of correctly maintaining and surveying steel wire ropes, and in particular the issues associated with encasing steel wire ropes in plastic sheathing on life-saving appliance (LSA) slings. SOLAS requires that falls used in launching are inspected periodically, and that launching appliances are…
DNV GL Issues RP on Offshore Fiber Ropes
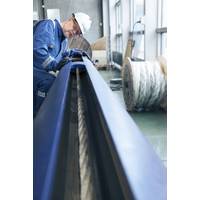
The results of two DNV GL led joint industry projects (JIPs) and a JIP pre-study commissioned by Statoil are now captured in a new Recommended Practice (RP) on offshore fiber ropes. With a system perspective on mooring performance, DNVGL-RP-E305 provides new industry guidance for achieving cost reductions of overall mooring operations, by addressing the engineering, manufacture and integration of offshore fiber ropes.
United Offshore Services and Samson Unite
Samson and United Offshore Services (UOS) announced a partnership to supply Samson high-performance synthetic ropes to Europe. This expansion of the UOS product offering is driven by the increasing demand from their customers who recognize and value the advantages of heavylift slings made with synthetic rope. Samson manufactures high-performance synthetic rope from its production facilities in the United States. With a history reaching over 130 years…
LNG Mooring Lines Made with Dyneema
The introduction of new and larger vessels, Q-Flex and Q-Max, and new, often more exposed terminals becoming operational have changed mooring dynamics. The need to maintain workers’ safety at all times, whilst delivering maximum operational efficiency through lower costs and faster turnaround times remains unchanged. DSM Dyneema, a close partner to the LNG industry, has done a study which concludes that these industry trends are changing the performance demands for LNG mooring lines.